
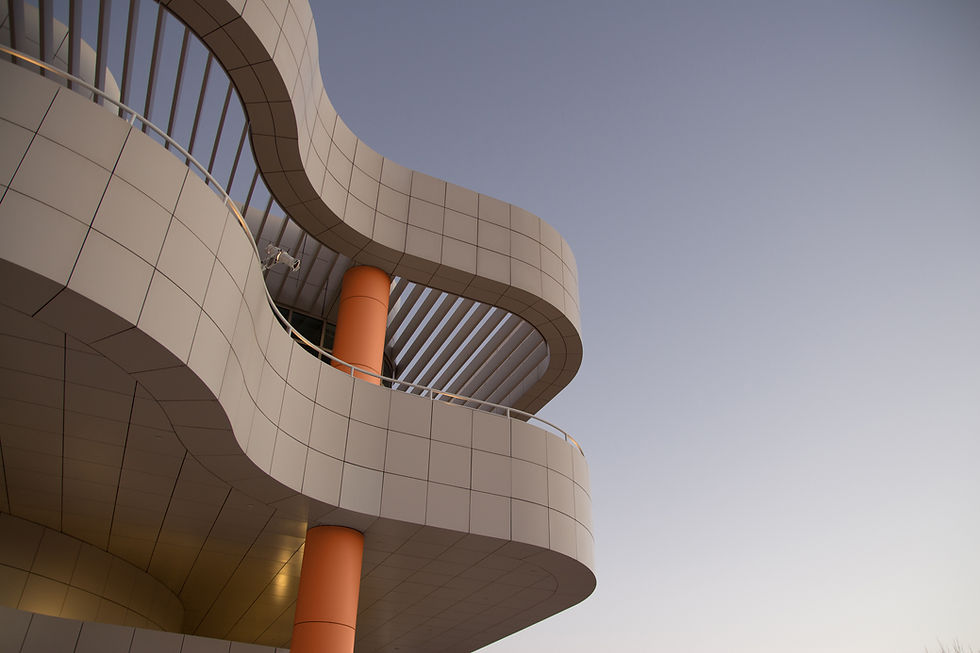
Choosing the Right Stainless Steel Welding Method: TIG vs. MIG
Mar 18, 2024
2 min read
0
24
Stainless steel welding is a critical aspect of fabrication across various industries, from automotive to aerospace. Among the most popular methods are Tungsten Inert Gas (TIG) and Metal Inert Gas (MIG) welding. Each technique offers distinct advantages, particularly when working with stainless steel. Let's delve into the benefits of TIG welding versus MIG welding for stainless steel applications.
TIG Welding Stainless Steel: Precision and Control
TIG welding employs a non-consumable tungsten electrode to create the weld, along with an inert gas shield to protect the weld pool. When it comes to welding stainless steel, TIG offers several notable advantages:
Superior Aesthetic Finish: TIG welding produces clean, precise welds with minimal spatter. This makes it ideal for applications where aesthetics are crucial, such as architectural structures, food processing equipment, and medical devices.
Precise Heat Control: TIG welding allows for precise control over the heat input, minimizing distortion and preventing warping of thin stainless steel materials. This precision is particularly beneficial when welding intricate or thin sections, ensuring the integrity of the final product.
Versatility: TIG welding can be used with a wide range of stainless steel alloys and thicknesses, offering versatility across various applications. Whether welding austenitic, ferritic, or duplex stainless steel, TIG provides consistent and reliable results.
Weld Quality: TIG welding produces high-quality, defect-free welds with excellent mechanical properties and corrosion resistance. This makes it suitable for critical applications where weld integrity is paramount, such as pressure vessels, pipelines, and aerospace components.
MIG Welding Stainless Steel: Efficiency and Speed
MIG welding, also known as Gas Metal Arc Welding (GMAW), uses a consumable wire electrode and a shielding gas to create the weld. While primarily known for its efficiency and speed, MIG welding also offers several benefits for stainless steel fabrication:
High Deposition Rates: MIG welding allows for high deposition rates, making it suitable for welding thicker stainless steel materials quickly. This efficiency is advantageous in industrial settings where productivity is a priority.
Ease of Use: MIG welding is relatively easy to learn and can be automated for increased efficiency. This makes it a preferred choice for high-volume production environments, where consistency and speed are essential.
Suitability for Thick Materials: MIG welding is well-suited for welding thicker stainless steel sections, providing deep penetration and strong weld joints. This makes it suitable for applications such as structural fabrication, heavy machinery, and automotive components.
Cost-Effectiveness: While TIG welding equipment can be more expensive, MIG welding tends to be more cost-effective, especially for large-scale projects. The lower equipment and labor costs make MIG welding an attractive option for budget-conscious fabricators.
Choosing the Right Method
In conclusion, both TIG and MIG welding offer distinct advantages for
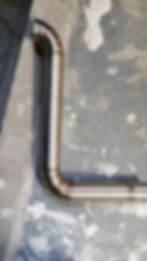
TIG welding excels in applications that require precision, aesthetics, and weld quality, while MIG welding shines in high-volume production environments, thicker materials, and cost-effectiveness.
Ultimately, the choice between TIG and MIG welding depends on various factors, including the specific requirements of the project, material thickness, desired weld quality, and budget constraints. By understanding the benefits of each method, fabricators can make informed decisions to achieve optimal results in their stainless steel welding endeavors.